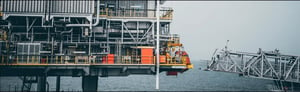
Supergrip
Consultants and experts in Polyurethane applications to the Oil, Gas & Energy Markets
With increased demands from the global oil and gas and energy industry, Nylacast acquired Supergrip Ltd in 2020 to expand its manufacturing capabilities and improve its knowledge of applications.
Supergrip is a business unit within Nylacast that is dedicated to guiding and consulting on projects within the industry. Each team member has extensive qualified experience solving complex challenges. We confidently consult on projects to examine the design, assess application performance when operating under stress, share our expertise on engineering polymer suitability for application and aid with installation.
The Supergrip business unit have a dedicated office for Engineering consultation, project delivery and onsite testing in Darlington, UK.
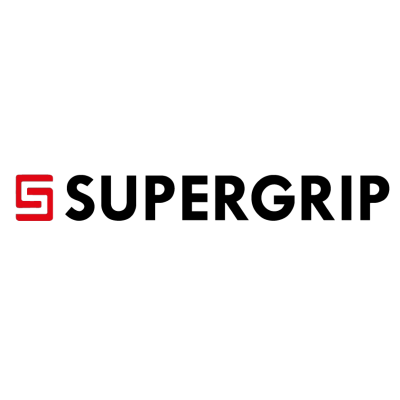
- YME Marine Operations
- Bahr Essalam
- Erin Oyo
- Jukes Group
- Gullfaks
- Troll C Riser
- Nemo
Supergrip Services:
Our team is dedicated to performance, efficiency and safety, therefore our in-house service include:
- Product, Engineering Design
- Bespoke solutions
- Concept development and feasibility reviews
- Project launch
- Project plan
- Resource Management, for on time delivery
- Manage risks and changes
- Monitor progress and performance, keeping the client informed
- Testing and quality compliance checks
- Maintaining budgets & ensuring high quality production
- Project delivery with optional installation support
- Full range of Engineering Polymers and metallics
- Material development supported by R&D testing
- CNC milling, turning and cut to size technology
- Polymer Casting
- Fabrication and welding
- NDT and inspection
- Quality Assurance and inspection
- Product assembly
- Factory acceptance testing (FAT) and qualifications
- Pressure and load testing
- Wet testing
- Material testing & verification
- Installation and operational testing
Clamping Solution Applications
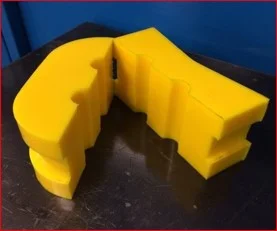
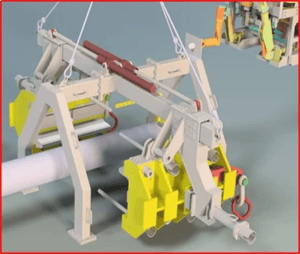
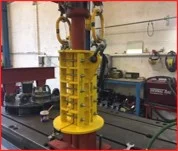
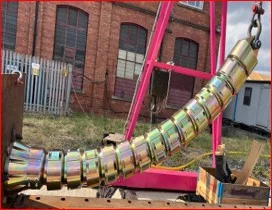
Cable Protection System Applications
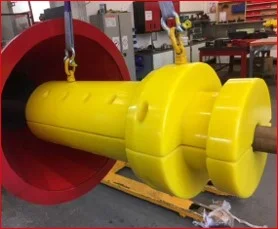
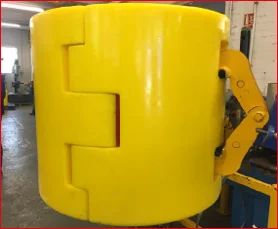
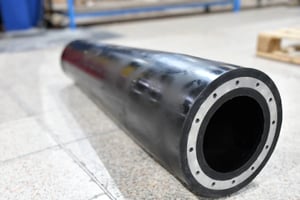
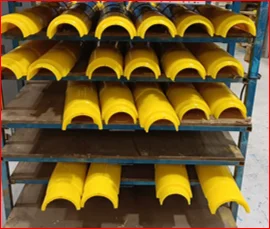
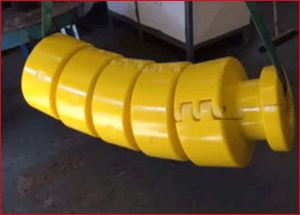
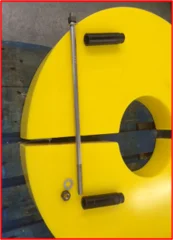
Sealing Solution Applications
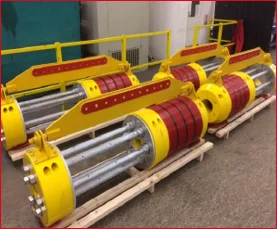
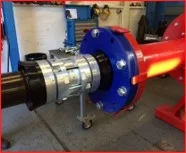
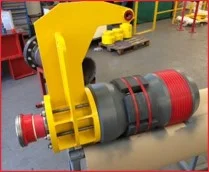
Problems we solve
- Active J-Tube Seal
- Bespoke Pull in head & Bend Stiffeners
Case Study: Enhancing Application Performance
Industry: Offshore, Oil & Gas, Renewables
Original Material: Steel
New Material: Nylacast Aquanyl 612
Challenge:
We were tasked with engineering and manufacturing a bespoke ROV activated J-Tube that would meet all the testing requirements to prove the equipment would be field ready for a challenging installation.
Solution:
This project resulted in a successful installation of the Active J-Tube Seal on the Tommeliten Alpha Development platform in the North Sea. The bespoke applications were delivered for the umbilical installation campaign by our team of offshore certified personnel who provided support & supervision to a global leader in offshore installations for the offshore assembly of the Active J-Tube Seal. The completion of this project, that was engineered & projected managed by our team, adds to our extensive track record in supplying Cable & Umbilical protection & sealing solutions.
Case Study: Enhancing Application Performance
Industry: Oil & Gas
Original Material: Steel
New Material: Metallic, stainless, carbon steel
Challenge:
Our Supergrip Team had been requested by JDR to provide a Non-Corrosive Pull-In Head Assembly for Hywind Tampen Project, the world’s largest floating offshore wind farm to date, which was suitable for 1 year subsea abandonment. Design requests included a 26-year design life, system minimum bend radius of 2.5m, static BSR included on exit point and 1mT maximum weight.
Solution:
Having utilised our in-house team of skilled engineers & project management, manufactured, assembled, tested & supplied a number of bespoke articulated pull-in heads & bend stiffeners which were successfully delivered to JDR Cables. The first of which was utilised during offshore installation.
Advantages:
- Increased Safety
- Custom Solutions
- Maintenance reduction