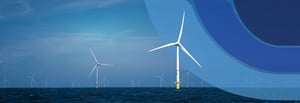
Renewables
Energising Sustainability: Advanced Polymer Solutions for Renewables
Enhancing your technology with Engineered Solutions
As the demand for renewable energy grows, OEMs and operators constantly require the technology to meet the highest specifications to generate the most significant output, whether wind, hydro, or tidal.
As project are high-pressure, equipment producers and operators require reliability, minimum downtime, high performance, and operational safety.
Nylacast is committed to application consultancy and material innovation to support the industry's need to enhance the renewable energy technologies. Our aim is to provide solutions that are specifically designed around reducing installation times.
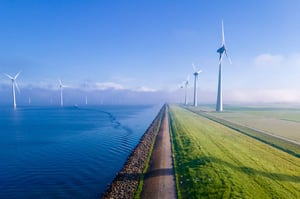
The Nylacast team provide brand solutions with:
- Nyalcast Engineered Products: Cast Nylon and other engineering Polymer solutions
- Supergrip: Polyurethane Solutions
Each team member has ample experience in the industry solving complex challenges. We confidently consult on projects to examine the design, assess application performance when operating under stress and share our expertise on engineering polymer suitability for application.
Examples of Projects Supplied
- Hywind
- Calvados
- Femcap
Industry Solutions
Nylacast's polymer solutions in renewables are engineered for excellence in safety, durability, and efficiency. Discover the unique advantages:
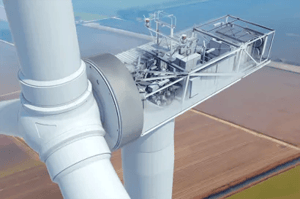
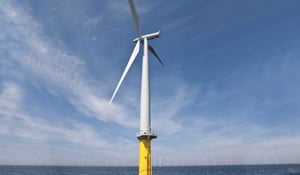
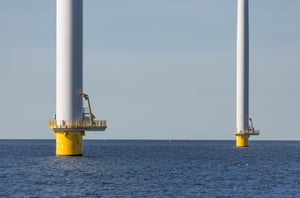
Cable protection systems, Buoyancy clamps, Cable entry joints, instrument / sensor collars, Bend Restrictors, and Floating anchor systems.
Nylacast Engineered Product Applications:
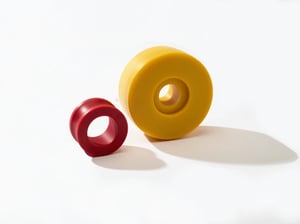
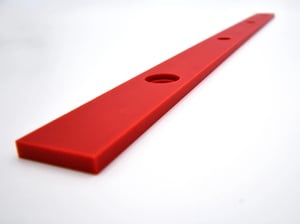
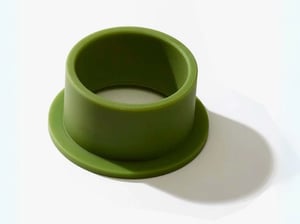
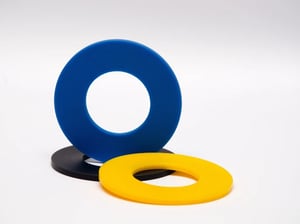
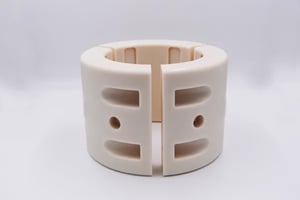
Supergrip Applications:
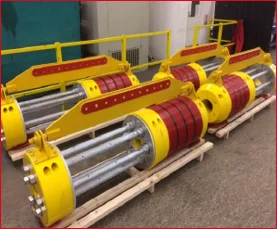
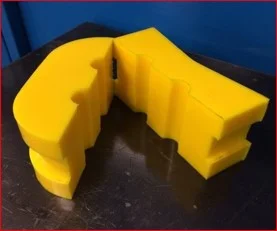
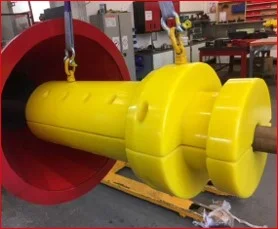
Providing solutions for the Renewable Energy Industry
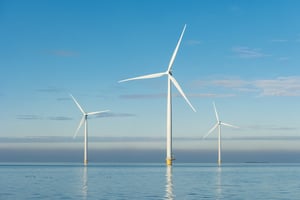
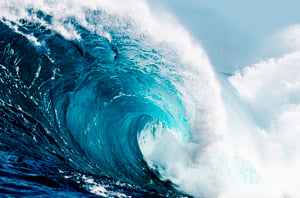
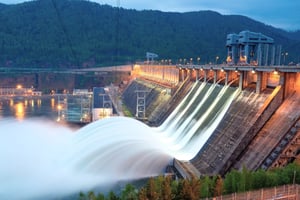
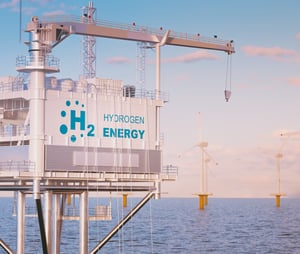
Problems we solve
- Bespoke Pull in head & Bend Stiffeners
Case Study: Enhancing Application Performance
Industry: Offshore, Oil & Gas, Renewables
Original Material: Steel
New Material: Metallic, stainless, carbon steel
Challenge:
Our Supergrip Team had been requested to provide a Non-Corrosive Pull-In Head Assembly for Hywind Tampen Project, the world’s largest floating offshore wind farm to date, which was suitable for 1 year subsea abandonment. Design requests included a 26-year design life, system minimum bend radius of 2.5m, static BSR included on exit point and 1mT maximum weight.
Solution:
Having utilised our in-house team of skilled engineers & project management, manufactured, assembled, tested & supplied a number of bespoke articulated pull-in heads & bend stiffeners which were successfully delivered. The first of which was utilised during offshore installation.
Advantages:
- Increased Safety
- Custom Solutions
- Maintenance reduction
Contact Our Experts
.png?width=300&name=Untitled%20design%20(3).png)
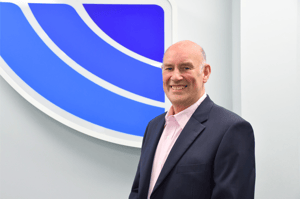
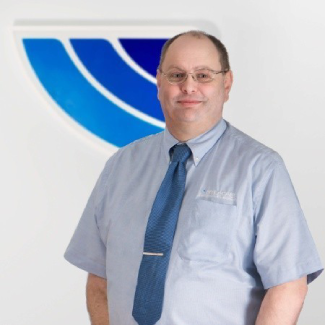
.png?width=300&name=Copy%20of%20Untitled%20Design%20(1).png)
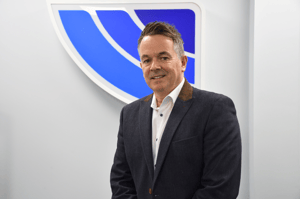