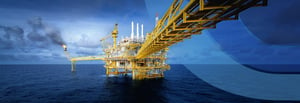
Oil & Gas Offshore
Offshore Innovations: Powering The Oil & Gas Industry with Polymers
Enhancing your technology with Engineered Solutions
In the demanding world of Oil & Gas, stakeholders and technology producers assess many factors to launch a project. For each project to be delivered successfully, the subsea pipeline equipment performance is vital.
Whether our clients are involved in shallow or deep-water pipeline installation, drilling, well construction, product extraction, deep water exploration, or asset maintenance, the need is ever evolving. Therefore, we collaborate with key market influencers to enhance technological performance and efficiencies, focusing on safety, minimising risk, reducing downtime and maintenance needs, and reducing equipment weight.
The Nylacast team is split between the three brand solutions:
- Nylacast Engineered Products: Cast Nylon and other engineering Polymer solutions
- Supergrip: Polyurethane Solutions
- Pipeline Engineering: Pipeline pigging and flow assurance products
Each team member has ample experience in the industry solving complex challenges. We confidently consult on projects to examine the design, assess application performance when operating under stress and share our expertise on engineering polymer suitability for application.
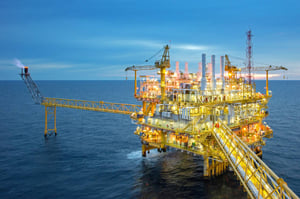
Industry Solutions
Nylacast delivers a range of advantages for the Oil & Gas sector, encompassing technical support in design and material selection, cost efficiency, durability, and safety. These key benefits include:
Corrosion resistant materials technology protects against the arduous environments.
Reduced and often eliminated need for additional and costly grease and lubricants through the use of low friction materials technology.
Engineered products custom developed for specific application need from initial chemistry to end product.
Nylacast Engineered Product Solutions
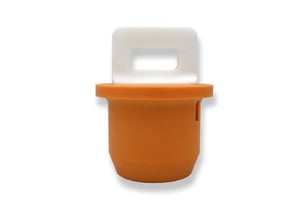
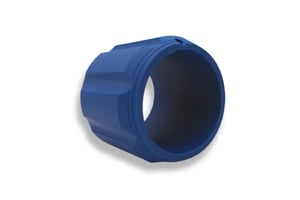

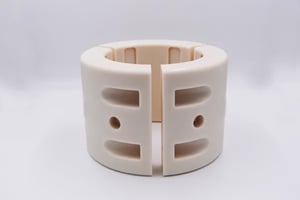
Supergrip Solutions
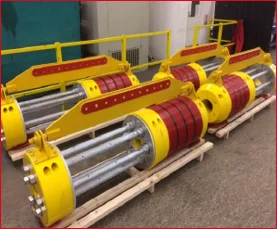
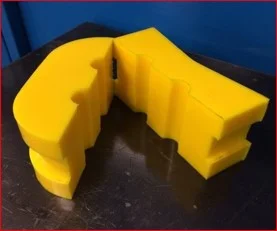
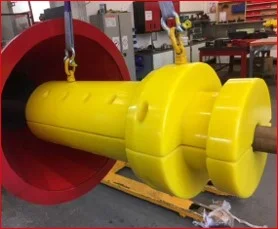
Pipeline Engineering Solutions
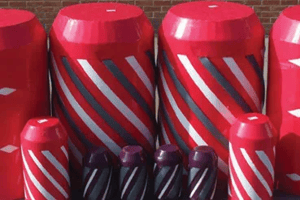
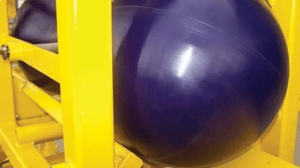
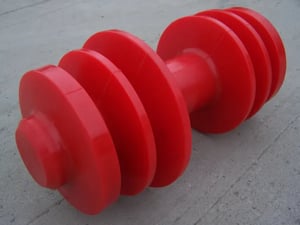
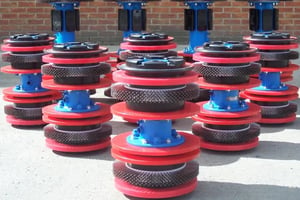
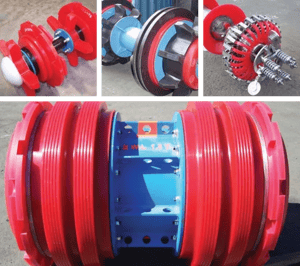
Box Description
- ROV Buckets
- Downhole Centralisers
Case Study: Enhancing Application Performance
Equipment: Subsea Trees, Manifolds, Subsea Connectors
Industry: Oil and Gas
Original Material: Metallics
New Material: Polyamide Alternative ROV Torque Bucket
Challenge:
Corrosion, multiple coating processes, and the elevated weight of component posing challenges in terms of handling and installation.
Solution:
Tailored polyamide material formulation for specific application functions, resulting in a considerable weight reduction compared to the conventional metallic version. Enhanced ease of handling, elevating operational efficiency.
Advantages:
- Decreased weight
- Low water absorption rate
- Cost competitive compared to metallic version
Case Study: Enhancing Application Performance
Equipment: Downhole Drilling
Industry: Oil and Gas
Original Material: Metallic Centraliser
New Material: Polyamide Alternative Centraliser
Challenge:
Elevated friction and wear levels, coupled with substantial weight, leading to increased well construction costs and challenges in both the handling and installation phases.
Solution:
A polymer centraliser with low wear and low friction properties, custom-manufactured to support extended reach operations, offering versatility with various fin widths and outer diameters.
Sturdy, resilient, and capable of providing outstanding performance.
Advantages:
- Light weight
- Zero corrosion
- No requirement for expensive synthetic & oil-based downhole fluids
Contact Our Experts
.png?width=300&name=Untitled%20design%20(3).png)
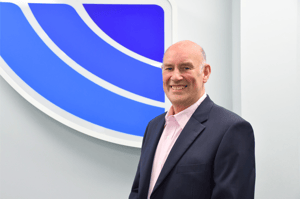
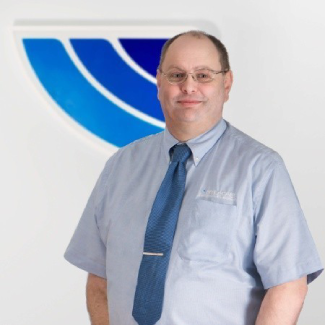
.png?width=300&name=Copy%20of%20Untitled%20Design%20(1).png)
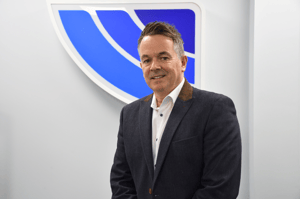